Step-by-Step Guide to Implementing a Quality Management System
Understanding a Quality Management System
A Quality Management System (QMS) is a structured framework that documents processes, procedures, and responsibilities for achieving quality policies and objectives. It helps organizations coordinate and direct activities to meet customer and regulatory requirements while improving effectiveness and efficiency continuously. Implementing a QMS can significantly enhance the quality of products or services, customer satisfaction, and operational performance.
Before diving into the implementation process, it's crucial to understand the fundamental components of a QMS. These include quality objectives, quality manual, procedures, work instructions, and records. Each component plays a vital role in ensuring an organization's quality standards are met consistently.
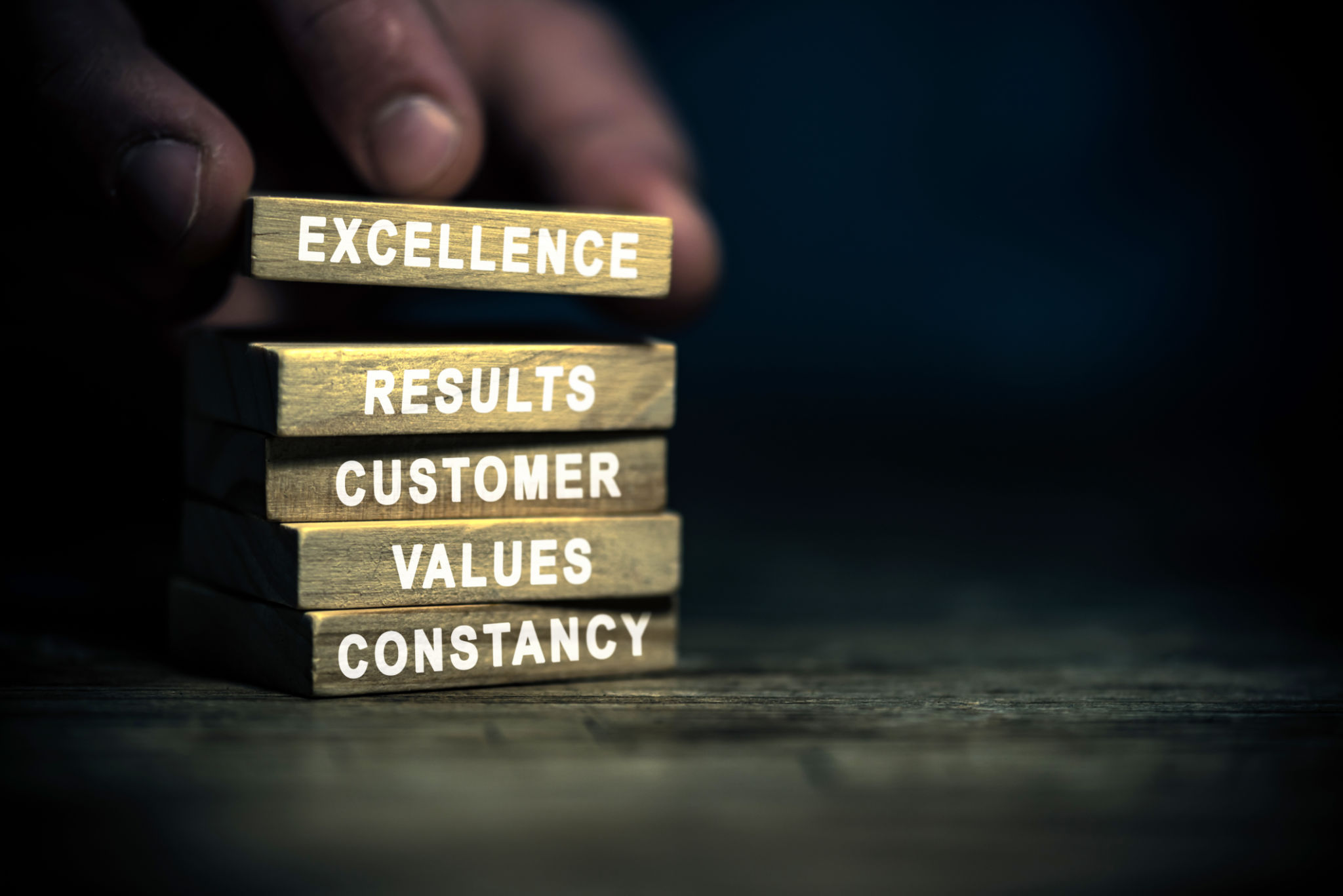
Initial Assessment and Planning
The first step in implementing a QMS is conducting an initial assessment. This involves evaluating the current processes and identifying areas that need improvement. Understanding where the organization stands will help tailor the QMS to address specific needs and gaps.
Once the initial assessment is completed, the next step is planning. Set clear objectives that align with both business goals and customer expectations. It's essential to involve key stakeholders during this phase to ensure comprehensive input and understanding. Planning should also include defining roles, responsibilities, and timelines for implementation.
Designing the QMS Structure
With a solid plan in place, it's time to design the QMS structure. This involves creating a quality policy that outlines the organization's commitment to quality. The policy should be communicated across all levels of the organization to ensure everyone understands its significance.
Next, develop a quality manual that serves as a guide for implementing and maintaining the QMS. It should include procedures, work instructions, and records management systems tailored to your organization's needs. The quality manual acts as a blueprint for achieving and maintaining quality standards.
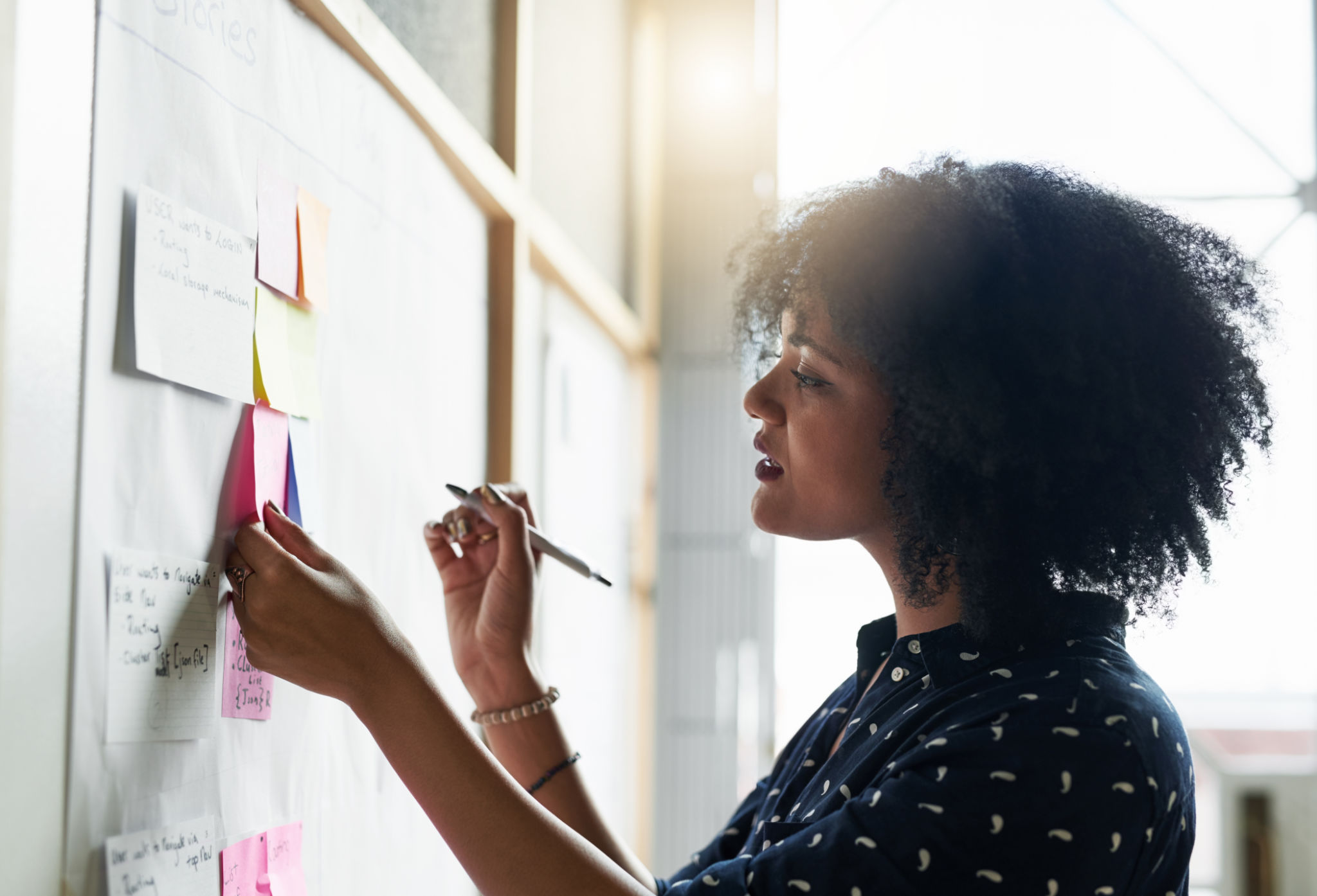
Implementation of Procedures
Implementing procedures is a critical phase in establishing a QMS. Begin by documenting standard operating procedures (SOPs) that detail how tasks should be performed to meet quality standards. Ensure these procedures are clear, concise, and accessible to all employees involved in relevant processes.
Training plays a crucial role during this stage. Employees need to be adequately trained on new procedures and understand their roles in maintaining quality. Conduct regular training sessions and provide resources to support employees in adapting to new processes.
Monitoring and Continuous Improvement
Once the QMS is implemented, continuous monitoring is essential to ensure its effectiveness. Regular audits and assessments help identify any deviations from quality standards or areas needing improvement. Establishing key performance indicators (KPIs) can provide measurable insights into how well the QMS is performing.
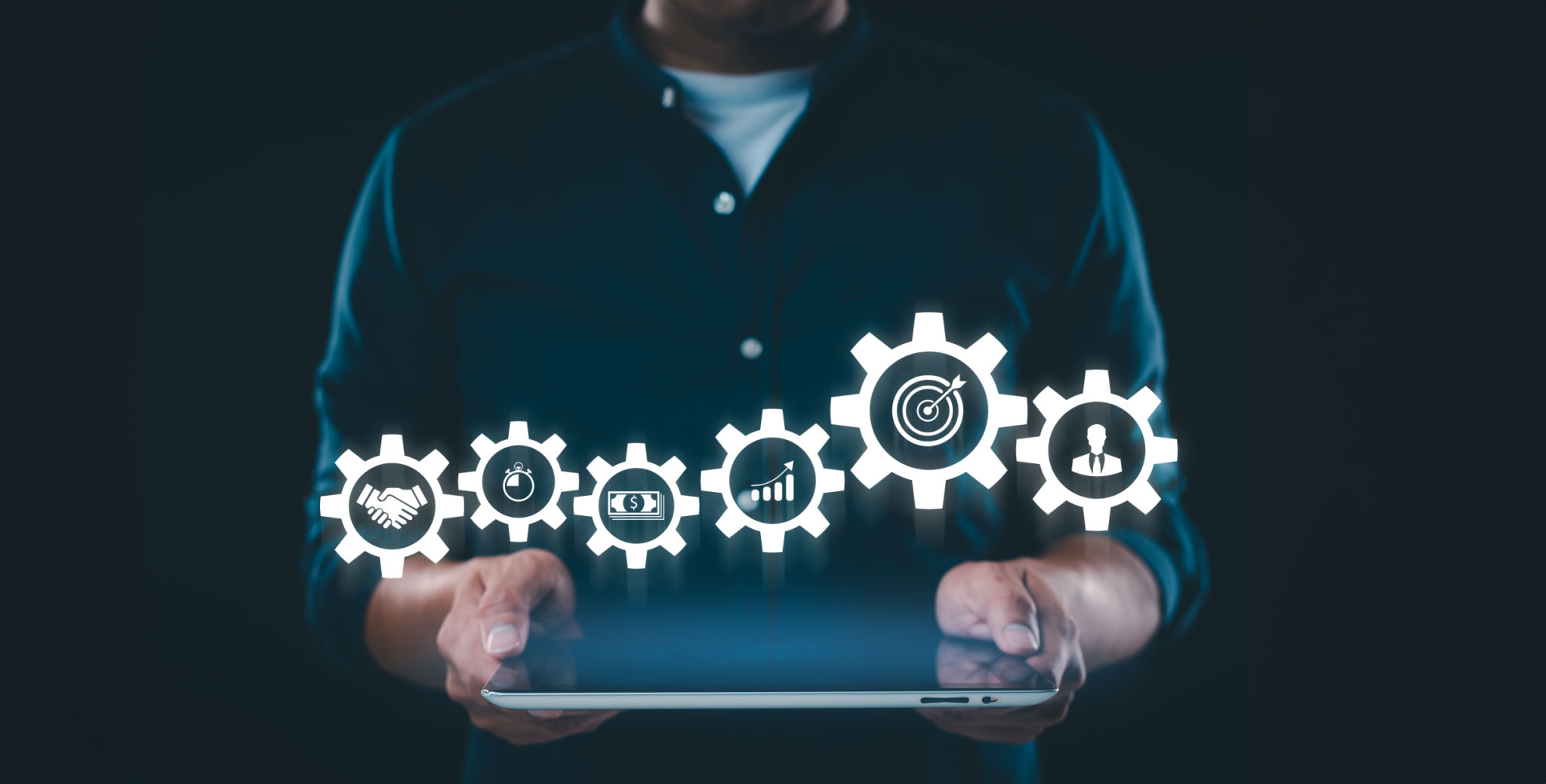
Continuous improvement is at the heart of any successful QMS. Encourage feedback from employees and customers to identify opportunities for enhancement. Implement corrective actions as needed and continually refine processes to maintain high-quality standards.
Review and Certification
The final step in implementing a QMS is undergoing a review and, if applicable, certification process. Conduct internal audits to ensure compliance with established procedures and evaluate overall system performance. Address any non-conformities before seeking external certification.
Obtaining certification from recognized bodies can enhance credibility and demonstrate commitment to quality. Certification also assures customers of the organization's ability to consistently deliver products or services that meet their needs.
In conclusion, implementing a Quality Management System requires careful planning, execution, and ongoing evaluation. By following these steps, organizations can achieve greater efficiency, customer satisfaction, and competitive advantage through improved quality processes.